季節によって起こる事故のパターンがある
夏、温度が上がれば気温は上がる。化学物質は、温度が上がると反応を始めるのが一般的だ
つまり夏になると温度上昇で事故が起きやすくなる
温度に敏感な物質の一つに過酸化物というのがある。反応開始剤や、塗料の硬化剤などに使われる
少ない量で使われることから、あまり危険と感じず使われている事例が多い
過酸化物起こった最大の事故は、爆発で9人の人が命を落としている。とんでもない爆発エネルギーがある
1990年5月26日に起きた事故だ
http://www.shippai.org/fkd/cf/CC0200059.html
高純度の過酸化物を小分けしていたときに起きた爆発事故だ。わずかに含まれていたメタノール蒸気に着火爆発した
こんな事故もある 2017/7/27 千葉県の茂原にある化学工場で起きた火災だ
タンクに過酸化物を入れたものの、時間がかかり過酸化物の温度が計画よりも上がっていた
更にタンク内には冷却コイルはあったものの、上から下まで完全に冷却出来るようにはなっていなかった
冷却コイルよりはみ出した、過酸化物は冷えず温度が上がっていた
更に本来は、数日以内に消費されるはずが、試運転計画が遅れた
タンク内に、規定の温度を超える状態で保管されていた有機過酸化物が異常反応を始め事故になったのだ
https://www.youtube.com/watch?v=SZ6mWKQsSfc
この企業では、2012年にも他の工場で有機過酸化物の爆発死亡事故が起きている
https://www.khk.or.jp/Portals/0/resources/activities/incident_investigation/hpg_incident/pdf/2012-106r2.pdf
有機過酸化物を甘く見ていた事故事例だ
とにかく、有機過酸化物は冷やさなければ事故になる
種類によっては、屋外に外気温程度で反応を始めるものもある
自分の工場で有機過酸化物が使われていないか検証して欲しい
有機過酸化物を甘く見ないことだ
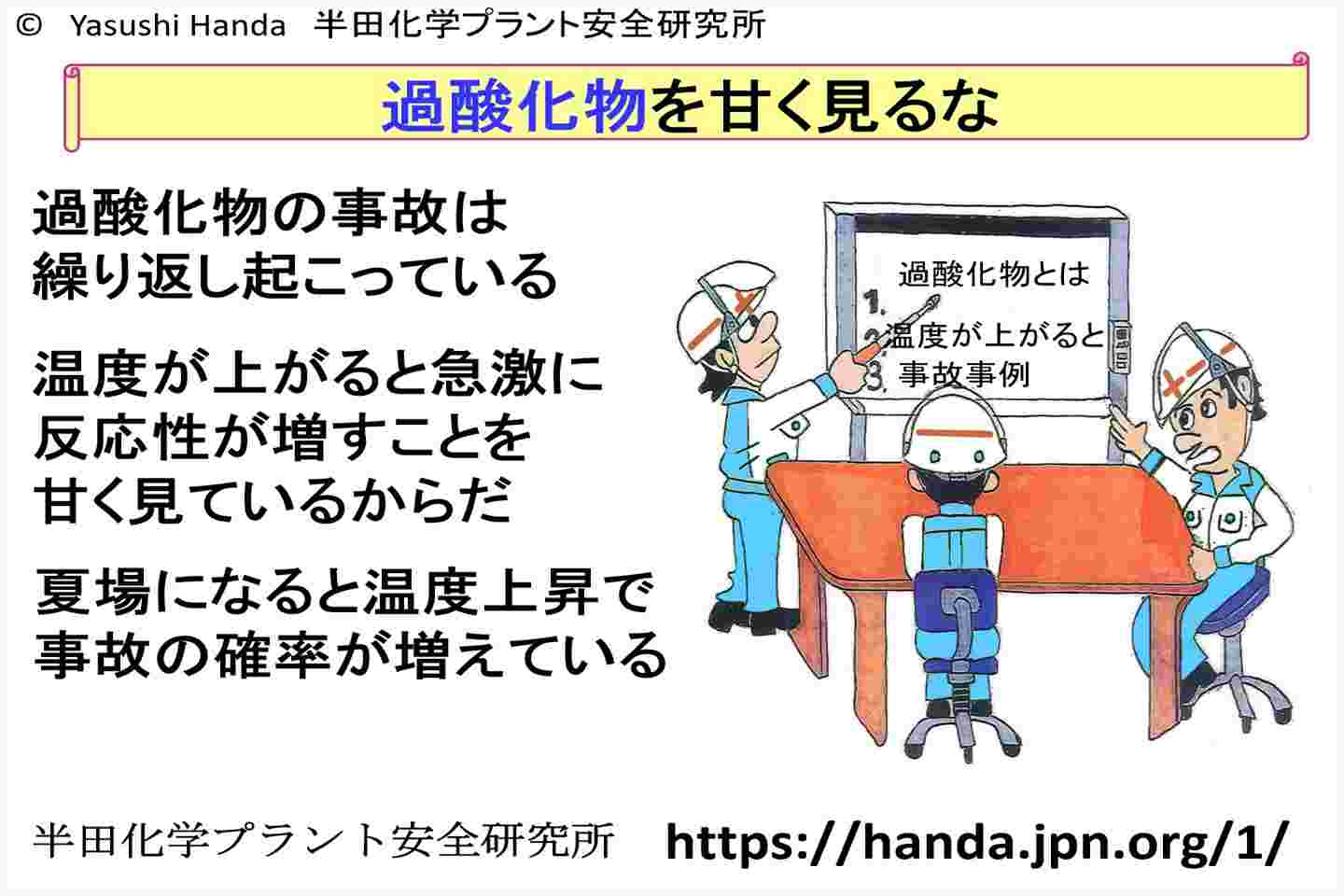