電気設備が原因で事故が起こることがある。事故の原因は、様々だが接触不良と老朽劣化が多い
https://www.jstage.jst.go.jp/article/ieiej/29/8/29_612/_pdf/-char/ja
電気は電線を伝って流れる つまりどこかで、電気装置と電線とつながる部分がある
そのつながる部分、いわゆる接続部に接触不良があると熱を持つ
温度が上がってしまうと、電線を包んでいる樹脂製の部分が溶けて燃えだしてしまう
電線の被覆は、難燃性のものもあるがコストが高いのでどうしても安い難燃性を持たないものが多用される
電線に火がつくと、最初はくすぶりながら周りに熱が広がっていく。そのうち、あっという間に周辺の電線に火がつき広がっていく
電線に油などが付着していると速いスピードで火災が進展する
電線を床の下にはわせる方式では、このケーブルダクトの中を見てみれば工場の電気火災に対する管理状態がわかる
2002年に宮崎県の化学工場で大きな電気火災事故が起きている
https://www.chem-t.com/cgi-bin/passFile/NCODE/10610
当時の安全担当者に聞いたことがあるが、工場の人達は、まさかケーブルが燃えるとは思っていなかったというコメントがある
大きな間違いだ ケーブルが燃えると相当な発熱量がある しかも、延焼するから広範囲に燃える大火災になる
電線を覆っているプラスチックやゴムの燃焼熱量は、ガソリンの燃焼とさほど変わらないと言われているからだ
この電気火災では大火災となり周辺住民を大量に避難させる事故であった
通報が遅れたことも原因だ。課長が消防への通報指示はすぐに出したが、誰が通報するということが決められていなかった
誰かが通報したと皆が思い込んでいて、結果として通報が遅れてしまった
通報者を決めておかなかったのが、通報遅れによる被害の拡大につながった
もう一つ地下のケーブルダクトに大量の油があったことも要因だ
この工場では、機械に使われている油が地下のケーブルダクトに時間をかけて流れ込んでいた
ところが誰もその油が危険とは思い込んでいなかった。電気火花で当然油にも火がついてしまった
時間が経ってからケーブルの接触不良が起こることもある
新設時のねじの締め付け忘れや、締め付けのもれが時間が経ってから問題を起こす
1970年代に会社に入った頃は良くケーブルの増し締め作業を定修時にしていたのを覚えている
20年~30年経過した電源設備は老朽化という問題もある
私のブログでも何回か電気設備の老朽化の話をしているので検索してみるといい
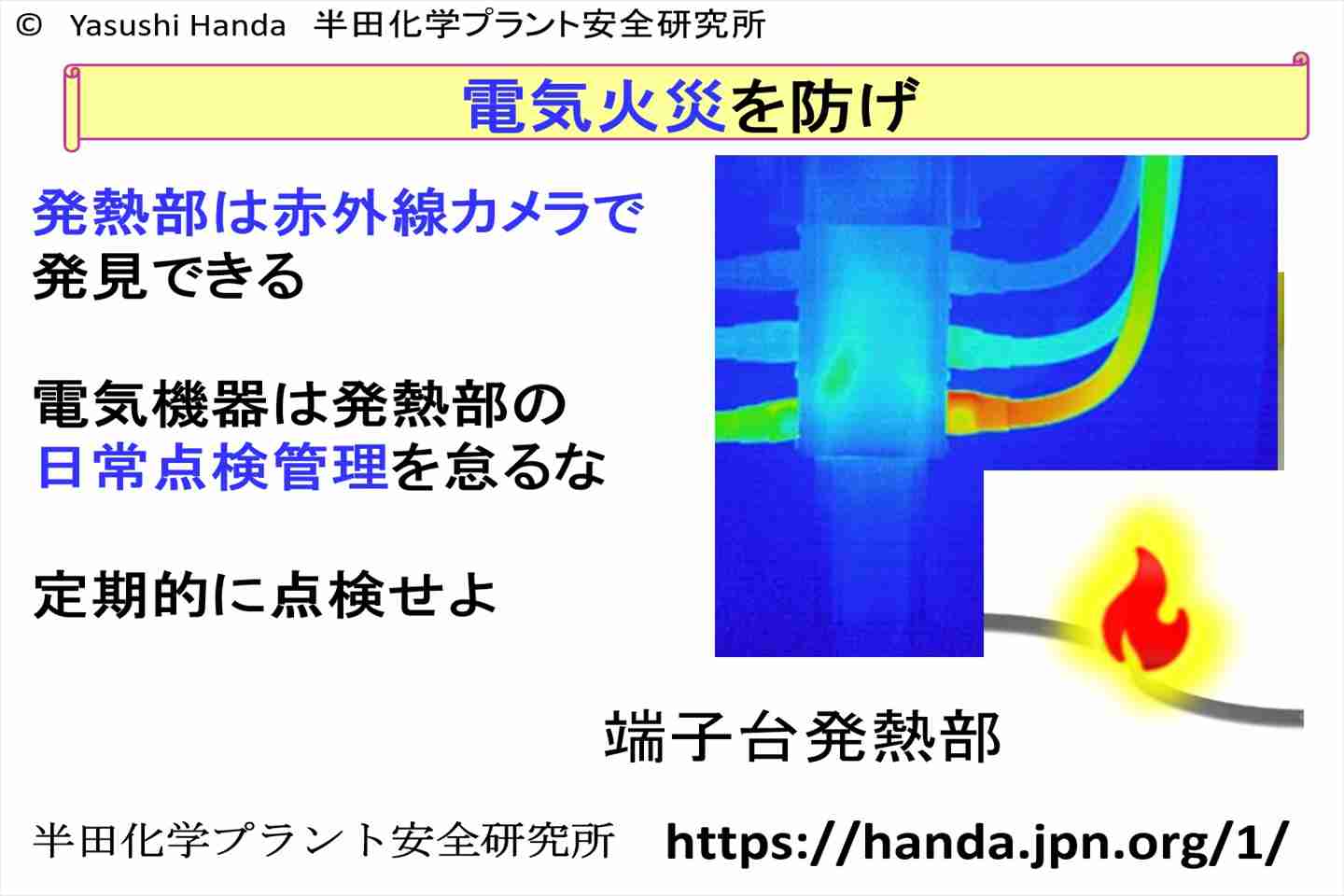