連続プロセス系とバッチ系の違い--事故の発生確率
化学プラントを見ると、バッチプロセスと連続プロセスがある
バッチプロセスというのは、容器に原料を入れ、何か反応とか混合をして、1回1回製品を作り上げる手法だ
原料を入れたり、温度を上げたり、撹拌をしたり人が色々とめんどうを見てやる必要がある
バッチプロセスは人が関与することが多い。人はミスを犯すから、どこかでトラブルが起こる確率は高い
連続プロセスというのは、人が関与せずかなりの部分が自動化されているので当然ヒューマンエラーが起こる確率は少ない
昔は、人件費もそれほど高くはなかったので、バッチプロセスが主流だった
ところが、人件費が上がるにつれ連続プロセスが主流になっていった
では、バッチプロセスの事故を見て見るととんでもない事故が過去起こっている
バッチプロセスというのは、同じような設備が存在することが多い
連続的に生産できないのだから、反応器は一つではない。何十個の反応器を設置して、切替えながら生産していくことになる
ある反応器は生産をさせているが、隣の反応器は生産を終え内部の清掃をしていることもある
つまり、生きている反応器と使っていない反応器が隣り合わせの状態で化学プラントが動いているのだ
現在のように、運転状態を監視できるモニターがしっかりと現場にあれば事故は起きないが昔はそうでは無かった
おまけに、運転員同士の連絡手段は今のように無線通信はなかった
そこで、すこしでも連絡がうまくいかないと、誤って生きている反応器でミスを犯すことになる
例えば、生きている反応器、つまり運転中の反応器のドレン弁を過って開いてしまう事故だ
たとえ、安全装置があっても人は、とんでもないことをする可能性はある
アメリカで起きた事故だがこんな事故がある。運転中の反応器のドレン弁の、安全蔵置を無視して強制的に開けた事故だ
大量の可燃物が吹き出し、5名の運転員が死亡した
https://www.youtube.com/watch?v=IRbC4kowrrY
https://www.csb.gov/assets/1/20/formosa_il_report.pdf?13838
日本でも、1960年代に同じような事故が九州の水俣にある塩ビ工場で起きている
バッチプロセスでは、人のミスをいかに抑えるかだ。バッチプロセスではヒューマンエラーを限りなく想定し、対策を打って欲しい
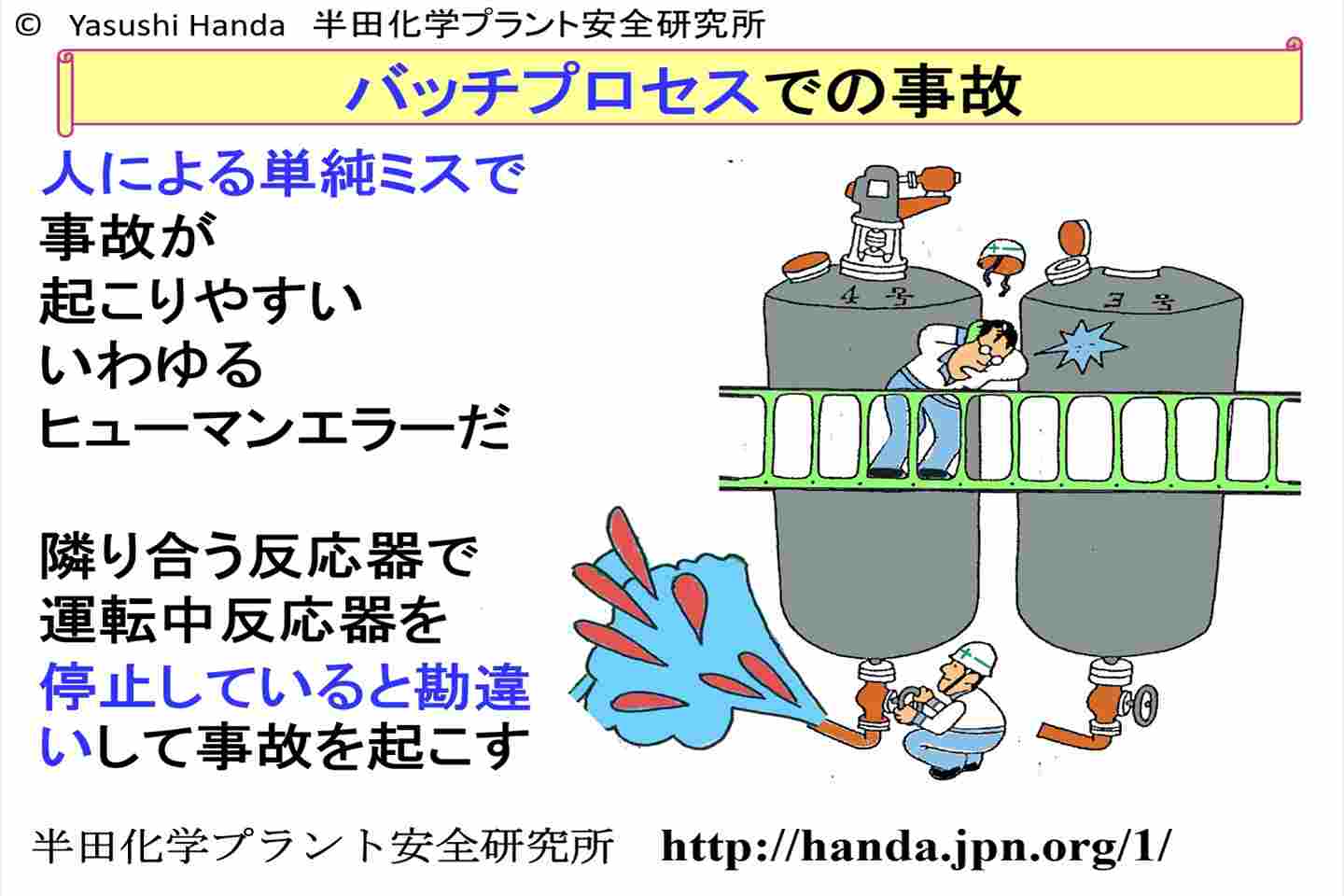