反応器で起こる事故--反応暴走
化学工場で起こる事故見て見ると、装置の種類によって事故のパターンというのがある
配管であれば、腐食漏洩。ポンプであれば、軸受け部からの漏洩や逆流。タンクであれば、底板腐食による漏洩などだ
今回は、反応器という装置に着目して事故のパターンを紹介してみたい
反応器であれば、最も怖いのは反応暴走だ
http://pe-eco.jp/articles/show/421/
発熱反応の物質であれば、冷却できなければこの反応暴走という現象が起こる
反応というのは、ある一線を越えると制御はできない。発熱量は、倍々ゲームのように指数関数的に増えるからだ
人間の手で何とかしようとすることはできない
今から10年前、当時勤務していた企業で爆発事故が起きた
山口県岩国にある工場で爆発事故が起きた まだ22才の若いオペレータが爆発で死亡した
過酸化物という温度に敏感な製品をつくる反応器が爆発したのだ。温度が上がり反応暴走した事故だ
http://tank-accident.blogspot.com/2013/01/2012.html
調査報告書によれば、一度作動させた反応器の安全インターロックを運転員が解除したことが事故の原因とされている
裁判でも、インターロックを解除したことで罰金刑をこの運転員が受けている
まだ22才の部下である運転員が死亡していることを鑑みると裁判官としてはこういう結論を出すのだろうが
事故の本質を見て見ると色々考えさせられることが沢山ある
工場の蒸気が一斉に停まったのが事故の発端だ 化学工場で通常、用役である蒸気が工場で停まることはあり得ない
蒸気を発生するボイラーを複数台常時動かし、蒸気が途絶えないようにするのが基本設計である
ところが、蒸気はある製造装置からの発生していた蒸気を有効利用していたから問題が起きた
つまり、ある一つの製造装置でトラブルが起これば全工場の蒸気に影響が出るという運転環境になっていたのだ
昔は蒸気の信頼性はかったかもしれないが、省エネだとか最適化だとかで結果的に蒸気供給の信頼性は落ちていたのだろう
そうは言っても、蒸気がなくなっても化学プラントで事故が起こるわけではない
安全に停止する設備は持っている 停止インターロック設備だ 今回もそれは正常に作動した
しかし、運転員はそのインターロックを解錠してしまった それは、思っていたほど反応器の冷却が進まなかったと感じたからという
もっと反応器の冷却能力に余裕があれば、事故は防げたのだろう。自分のプラントの冷却能力を検証して欲しい
事故のリスクを減らすために、反応器の冷却能力を上げることも考えて欲しい
冷却能力不足で起こる事例は多いからだ
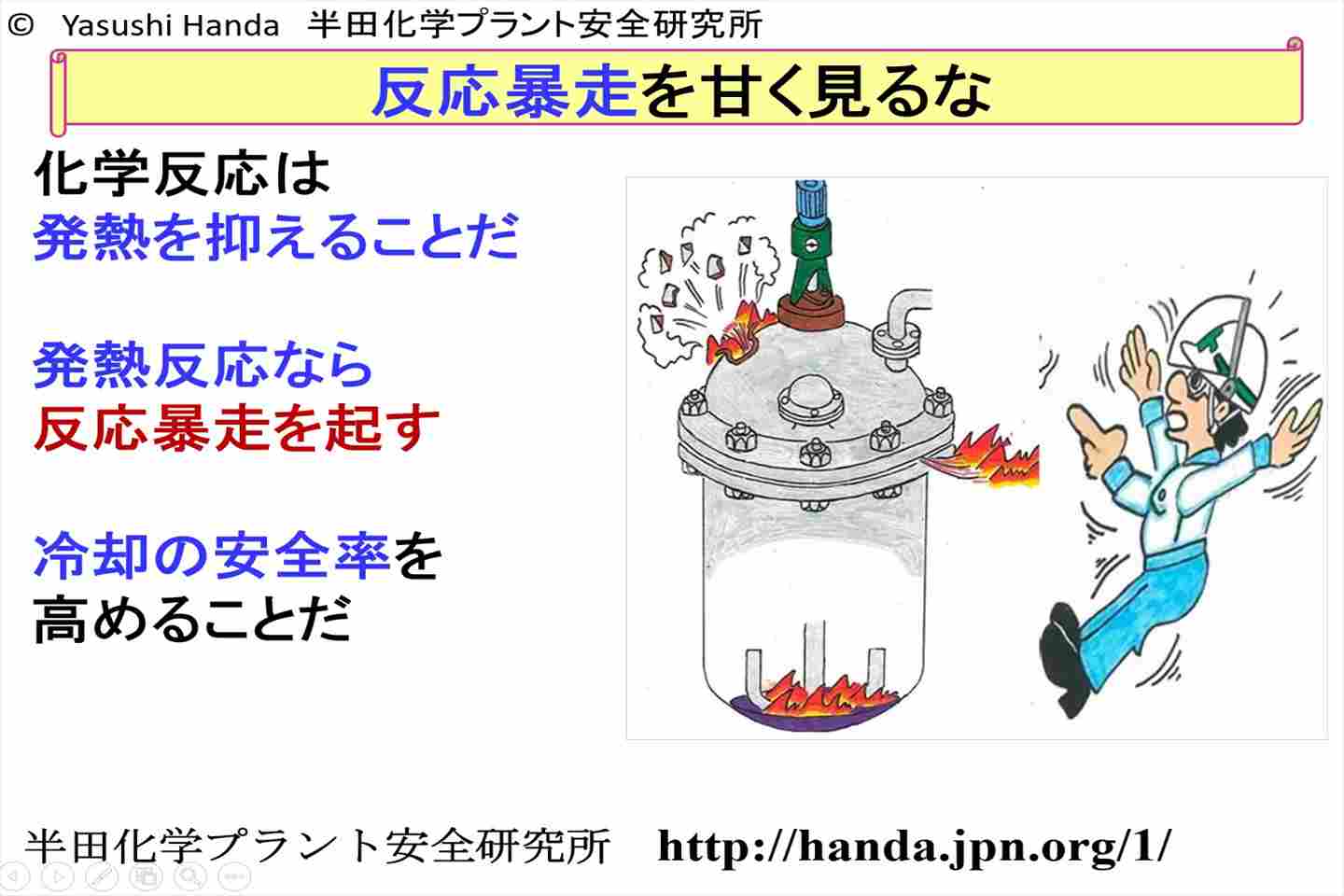