製油所の大規模火災に思う 事故の本質は何か
2017年1月22日に起きた和歌山の製油所で大規模火災が起きた事故を知っているだろうか
https://tank-accident.blogspot.com/2017/07/blog-post.html
https://www.eneos.co.jp/newsrelease/2017/20170614_01_1150234.html
製油所が数十時間に及ぶ大火災となった事故だ。住民も避難させられた大きな事故だ。
きっかけは配管が腐食して穴が開き、ガスが漏れ火災になったことだ。このガス漏れが起きたときは、地上高い所にある配管で大きな炎ではなかった
すぐに緊急停止システムは作動させたが、原料ポンプは自動的に停まる設計仕様にはなっていなかった
緊急停止はしたものの、原料ポンプが停まらなかったことで原料が流れ続け長時間最初にガスが漏れた配管開口部から大量の液が流れ続けた
原料ポンプをすぐに停められればこれほどの大事故にはならなかったはずだ
何が問題だったかを解き明かすと、緊急停止インターロック機能に問題があった
緊急停止インターロックに、原料ポンプの停止を組み込んではいなかったからだ
次の問題点は。原料ポンプは遠隔で停止出来る方式にはなっていなかったことだ
ポンプは現場で起動停止する方式で、計器室からの遠隔停止操作はできない方式だったというのだ
いわゆる現場操作型のポンプだ。火災発生時現場でなんとか停めようと試みたものの、炎でポンプの周りに近づけず現場で停止出来なかったという。
電気室に近づくことは考えたものの、電気室にも火が迫っていて結局電気室でポンプの電源SWを切れなかったという。
ポンプさえ停められれば、流れ出る油を停められ火炎は一気に抑えることが出来たと思われる。
この事故の教訓は何かと考えてみると、遠隔操作で原料ポンプを止められなかったことだ。
ポンプが停まらないから、配管に開いた穴からいつまでも可燃物が吹きだし長時間火災となったことだ。
火災が起きるととにかく現場に近づけない。電気室も火が迫ってしまえばこのような事態が起こる。
自分のプラントのどこかの配管が破れたら、現場に行かなくても安全に流出を早期に停められるような装置になっているか検証してみて欲しい
人が少なくなっている昨今は、いかに緊急時の自動化停止化や遠隔操作化を進めていくかだ
緊急遮断弁の増設も考える必要がある。漏洩範囲を極小化することによるよる効果も大きい
自分たちの設備が、省人化に対応した設備になっているか一度検証して欲しい。時代の変化に対応した設備管理が求められている
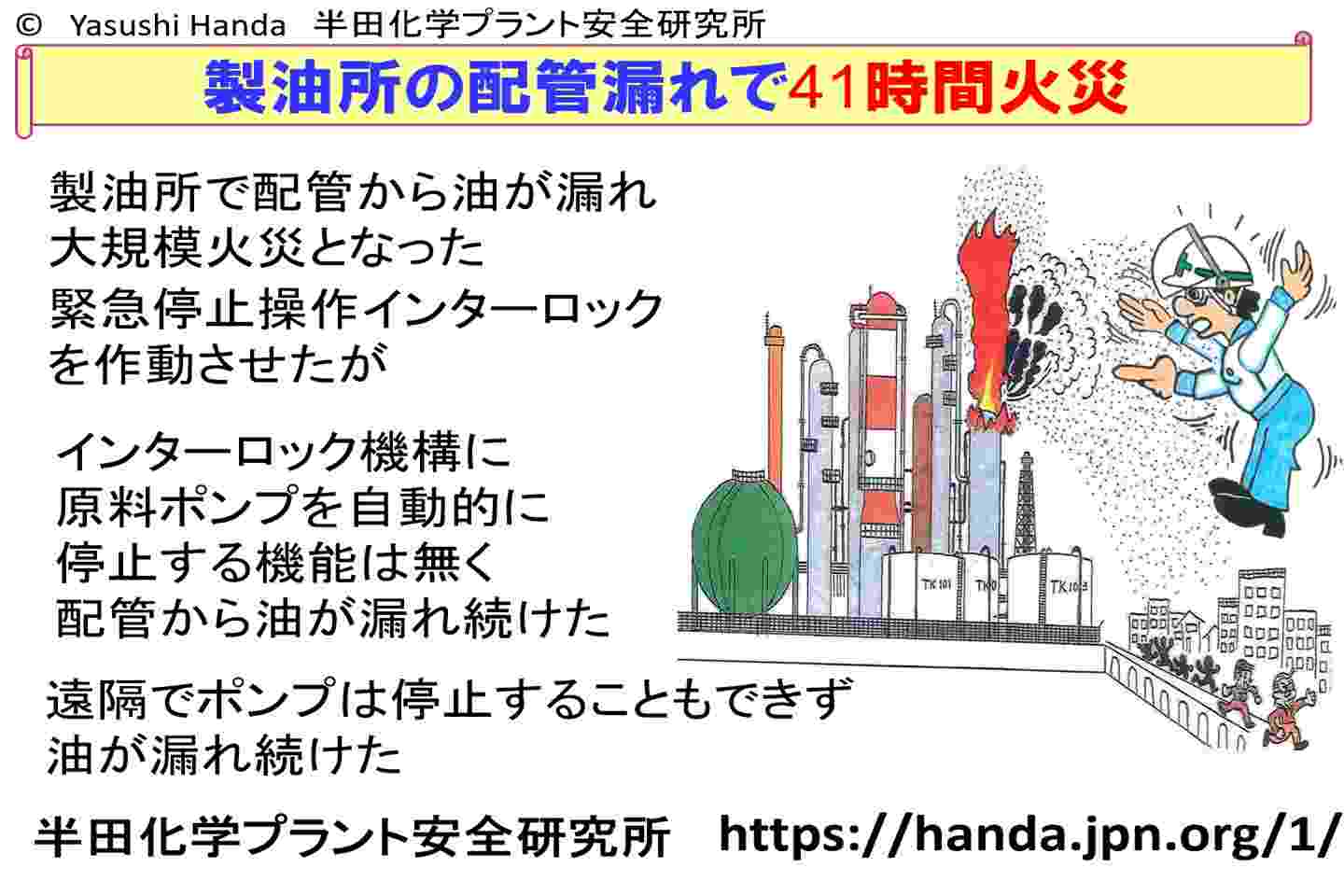